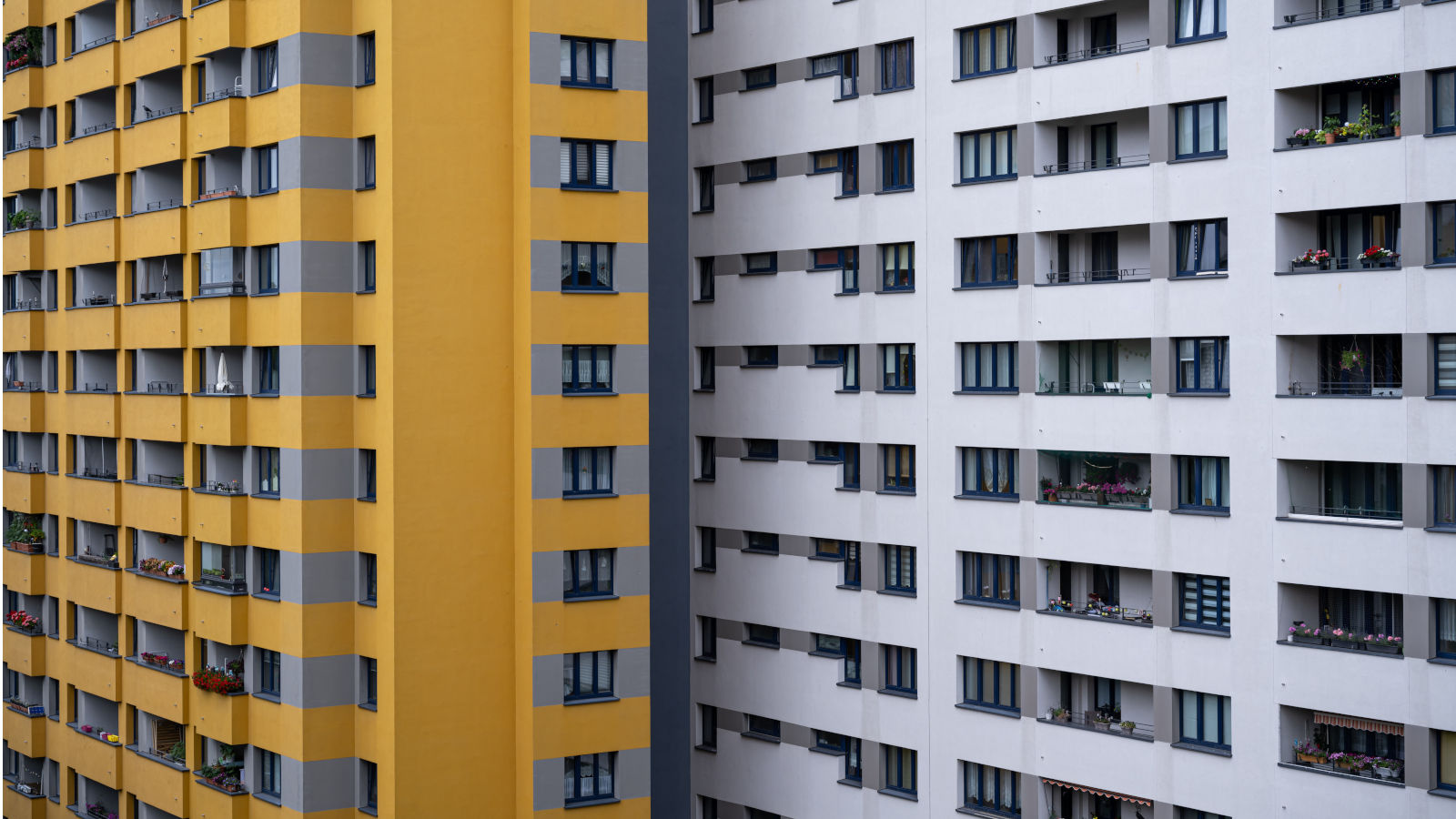
Building stocks will be increasingly raw material sources for different materials in the future. Based on building attribute data, it is possible to model and calculate material volumes in a building stock. When we know the volume materials, we can set targets like for the material utilisation rate of demolition waste, other environmental goals or renovation and even for the circular economy.
Few statistics are being kept on the share of use of different materials in construction around Europe. The shares of different materials in construction are only being tracked statistically in a few countries. Material-specific construction statistics should be developed and improved.
What complicates the compilation and modelling of the statistics is the versatility of the material used in construction. Construction is largely hybrid, which means that the shares and variables covered by statistics do not fully explain the overall use of materials. This applies to nearly all construction materials. For example, if a building is reported as timber-framed, it may still contain many other materials even in its load-bearing frame. On the other hand, a lot of wood may also be used in other building elements or secondary structures in non-timber-framed buildings.
A building is defined as a wooden building when its load-bearing frame material is mostly timber. The same definition applies to all buildings. This is the most common way of categorising buildings based on their material.
It is feasible to calculate material volumes bound in a building stock
Based on building attribute data, it is possible to model and calculate material volumes in a building stock with good accuracy. Building attribute and scope data provide the basis for calculating the numbers of different construction elements in buildings. By knowing the shares of different construction materials or structural solutions over the course of construction history, it is possible to deduce the proportions of materials used to the number of structures. By doing so, it is feasible to conclude the overall volumes for buildings and the entire building stock. The outcome can be checked against historical material use, as far as such data is available. In addition to building geometry, material usage depends on the other attributes of the unit, the most important ones being the building’s purpose of use and age.
Finland’s Euroconstruct member, Forecon, has studied and modelled the volume of key construction materials in the Finnish building stock. The volume of concrete and wood is very high as they are used in nearly all construction. In recent years, the annual use of concrete in construction has totalled approximately 5 million cubic metres, and approximately a million cubic metres of concrete is being demolished per year. As for wood, roughly 2.7 million cubic metres are used in construction on an annual basis. This covers material usage both in housebuilding, civil engineering and at construction sites.
Forecon is currently calculating the volume of plastic in the public service building stock built from 1970–1999. The volume of plastics in the building stock is around 0.5% of the weight of the materials. As such, the volume of plastic is minor in kilograms, but as recyclability improves, the economic and environmental impacts of recycled plastics may prove extensive.
Concrete dominates Finland’s building stock
The volume of concrete bound in the Finnish building stock is massive; according to a material volume calculation by Forecon, the built environment contains as much as 350 million cubic metres of concrete. Of this volume, 240 million cubic metres lie in the housebuilding stock. Concrete is the most commonly used material especially due to its strength properties but also because of its moderate price and durability. When talking about housebuilding and when calculated in constructed cubic metres, concrete as the main structural material covers nearly half of the entire building stock.
Concrete has been used in the Finnish building stock for a long time. In the early 1900s, concrete became more common, particularly in the foundations of apartment blocks and on base floors. The use of concrete in construction kept quite modest throughout the first half of the 1900s, however, until it began to become a lot more common in the 1950s and the 1960s. During that period, many current structural solutions started to gain popularity, including the bookshelf frame, concrete sandwich elements, massive intermediate floor elements and, slightly later, also hollow slabs.
“The amount of concrete refers to the concrete used in the building stock. The calculation is based on the building characteristics and is proportional to the use of cement and concrete at the time.”
Wood use in construction should be followed up more closely
In Finland, the share of timber construction is approximately 30%.
Approximately 45–50% of timber used in Finnish construction focuses on new construction, 30–35% on renovation, 8% on civil engineering and 12% on construction site use, mainly in new construction. In countries where timber use in structures (new construction) is fainter, the share of timber is accentuated in construction site use and in renovation.
The construction site use of timber covers various protective and support structures, moulds, accessways etc. Most of the timber is only used once, but some of it can be used several times.
In new construction, approximately 60–70% of timber products and volume used in Finland are accounted for by timber-framed buildings, which are classified as wooden buildings. Similarly, in renovation, timber use is presumably mainly focused on timber-framed buildings.
Also, the timber used in construction is highly centred around residential construction. In Finland, the timber used in residential construction accounts for approximately 70% of overall timber use in new construction.
In renovation, timber products in existing buildings are replaced by new timber elements. However, the amount of wood in buildings typically increases when renovated. In façades, for example, the share of timber increases during the building life cycle as façades are being renovated.
Timber is also widely used in small outbuildings and in the yard in general. In many countries, small outbuildings are excluded from construction statistics, but the timber use related to them is quite notable.
There is also willingness in the EU to invest in the tracking of materials used in construction. The use of woody biomass in construction in the EU should be monitored in more detail in the future.
Building stocks are increasingly raw material sources for different materials in the future
The environmental requirements for construction largely focus on new construction. The existing building stock should be included in these discussions more strongly than previously, however, as it affects decision-making to an increasing extent when it comes to renovation, the circular economy, energy or, for example, land areas to be vacated.
The demolition of buildings and the application of the so-called ‘demolition and new build’ method are still minor: annually, less than half a per cent of buildings are demolished in Finland. Going forward, demolition will increase, however, as the building stock is ageing and some of it is poorly located with regard to the population and business activities. ‘Demolition and new build’ will also become more common in areas where the value of the plot is high and there is a willingness to make the building stock denser. When demolishing buildings, materials are released into circulation.
Building stocks are increasingly becoming raw material sources for different materials in the future. Product manufacturers must use recyclable materials more than they are using today, and they must replace the use of virgin raw materials. In fact, a part of construction product manufacturers have taken steps in this direction, and there are now thermal insulation materials, different types of steel, aggregates and other products available on the market that are either partly or fully made of recycled materials.
Environmental perspective will also be highlighted in decision-making related to building stocks
In addition to new construction, it is also highly important to examine the material volumes and emissions in the existing building stock, from use to demolition and material reuse. Alongside new construction, the responsibility of major property mass owners and municipalities, for example, cannot be ignored in the pursuit of emission targets. Therefore, knowing the existing built environment and establishing the material volumes is key when assessing new emission targets and studying the impacts of low-carbon construction. Knowing the current state makes it possible to set the right type of emission targets and to analyse more realistically the actual impacts of the measures taken, covering the whole building stock.
A major share of building demolition materials is not recycled efficiently. Material sorting during demolition is challenging and expensive. Different materials are often attached to the same structures or individual products. As the need and demand for recycled raw materials increase, demolition techniques also develop further and make material sorting more cost-effective.
Concrete as a material does not burden the environment after demolition. Instead, with the right treatment, it starts to carbonate and rebind the carbon dioxide released into the air during limestone burning at the cement-making stage. The fairly good environmental factors of steel are based on the fact that steel is highly recyclable even today. The carbon dioxide contained in demolition materials burned for thermal energy is released at the end of the life cycle. These include wood and most plastics.
As regards building demolition, it is also important to examine the volumes of demolished materials and the shares of these materials eligible for recycling. When we know the expected volume of demolished materials, we can set targets for increasing the material utilisation rate of construction and demolition waste.
In the future, companies must report how big a share of their business follows the EU taxonomy. This may also mean that a taxonomy analysis is carried out on a property mass, which necessitates that the existing building stock is known. The analysis involves a calculation of the carbon debt, referring to the volume of greenhouse gases that the properties owned by the company have released into the air during their life cycles. The analysis covers both new construction and renovation projects. It would also be possible for an owner to examine its property portfolio according to material volumes and how a prospective new or demolished building would affect its construction material balance.